Our Production Methods
Die-Casting
This is a casting method for mass-producing high-precision, high-cycle castings with excellent surface finish by injecting molten metal into a precision mold. We have been making full use of various die-casting methods while adding our own original innovations to create products according to the shape and size of the product and the needs of the times. In recent years, we have been actively working to develop automotive body parts, chassis parts, and electrified parts as alternative applications for automotive engine and transmission parts. To this end, we are pursuing forms of manufacturing that are in demand among our customers by making full use of a wide variety of aluminum alloy materials. To further pursue the expectations and possibilities of aluminum alloy die-casting, in addition to equipment and robot technologies, we are actively working on peripheral process technologies including molten metal control technology, heat treatment technology, and welding and other joining technologies.
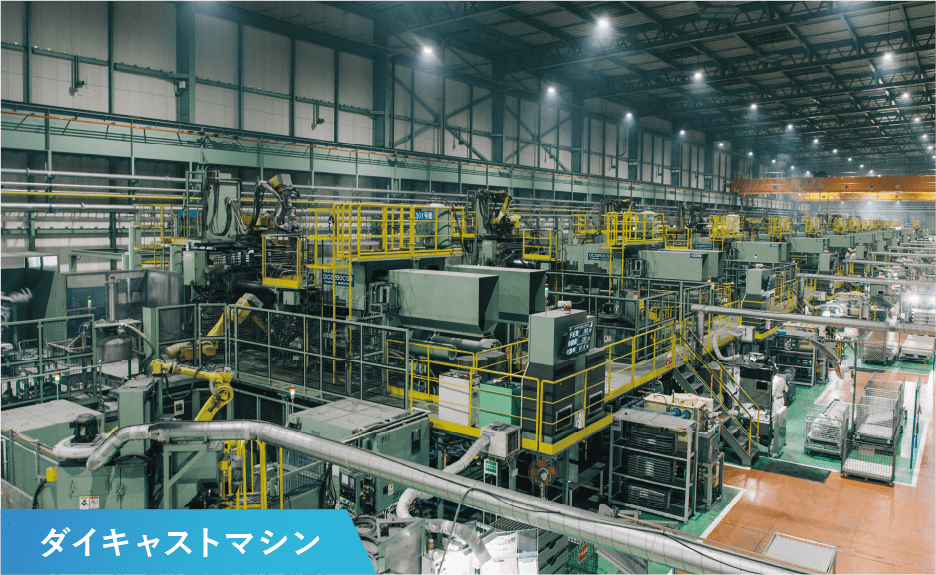
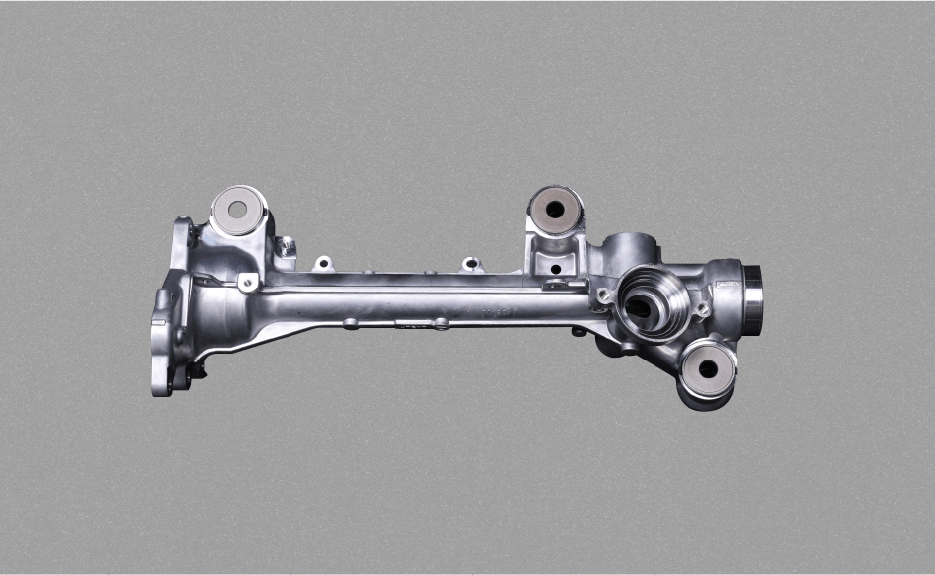
Sand Mold Casting
Sand mold casting is a traditional casting technique that has been in wide use since ancient times. Ever since our founding, we have been developing advanced production methods that take advantage of the superior characteristics of sand molds in our casting technology. Beginning with the casting of everyday utensils (pots and pans), for aluminum alloy sand mold casting, we have built an automated continuous molding and casting line using raw sand. This has allowed us to achieve mass production of aluminum alloy hollow castings such as automobile intake manifolds, as well as larger 6-cylinder intake manifolds. Sand mold casting is a production method that can be used to produce a wide variety of products in small quantities, and is also capable of manufacturing products that meet various needs and cost considerations.
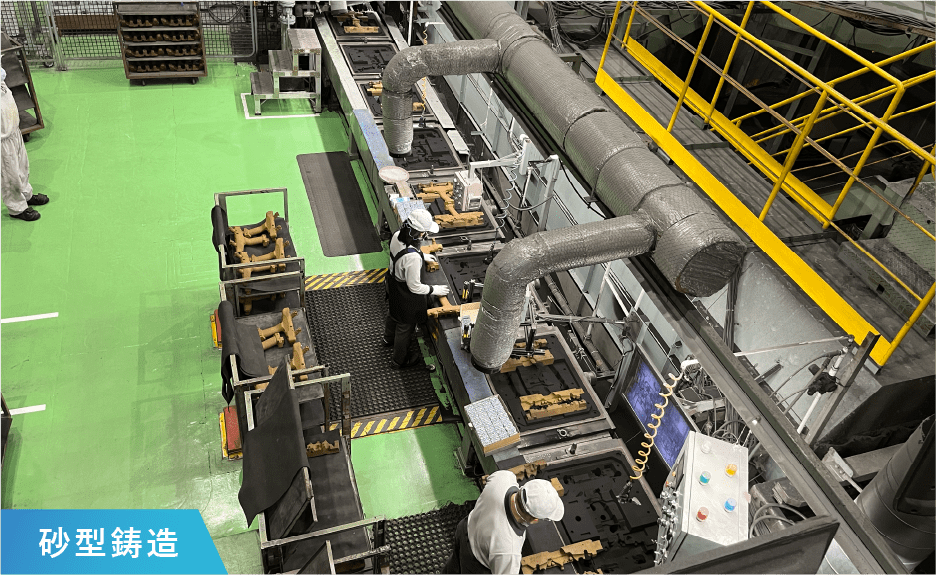
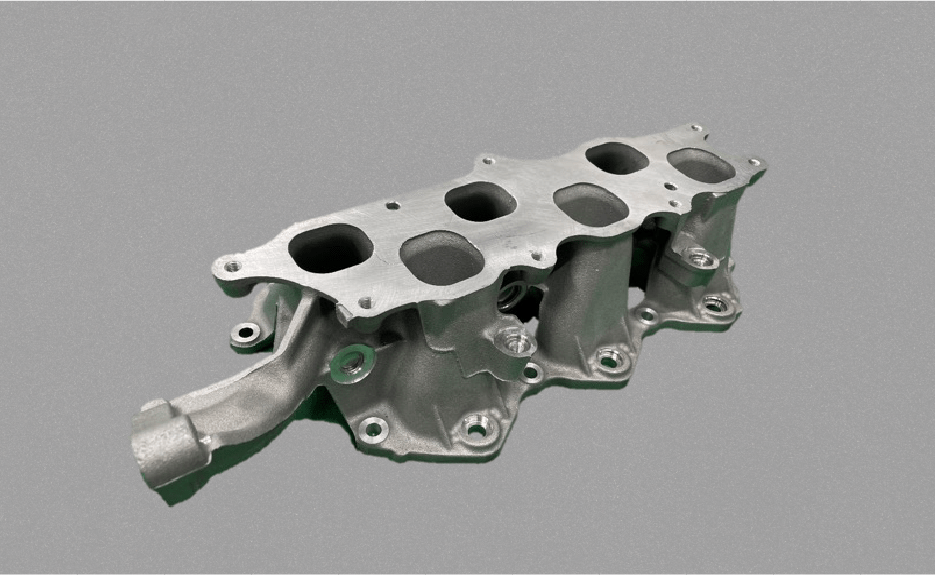
Gravity Die Casting
After sand mold casting, die casting is the next best choice for castings that require dimensional accuracy, such as household machinery parts. It also causes very few internal defects and is suitable for the production of high-quality castings, such as pressure-resistant parts for automobiles and agricultural machinery. Currently, we use gravity die casting exclusively for the production of our own brand of household utensils (pots and pans). Our thick-walled, high-quality aluminum cast pots and pans can withstand repeated heating loads without deformation, and have excellent heat-transfer characteristics.
This is how our accumulated knowledge and expertise in casting, cultivated throughout several decades, allows us to provide reliable household products.
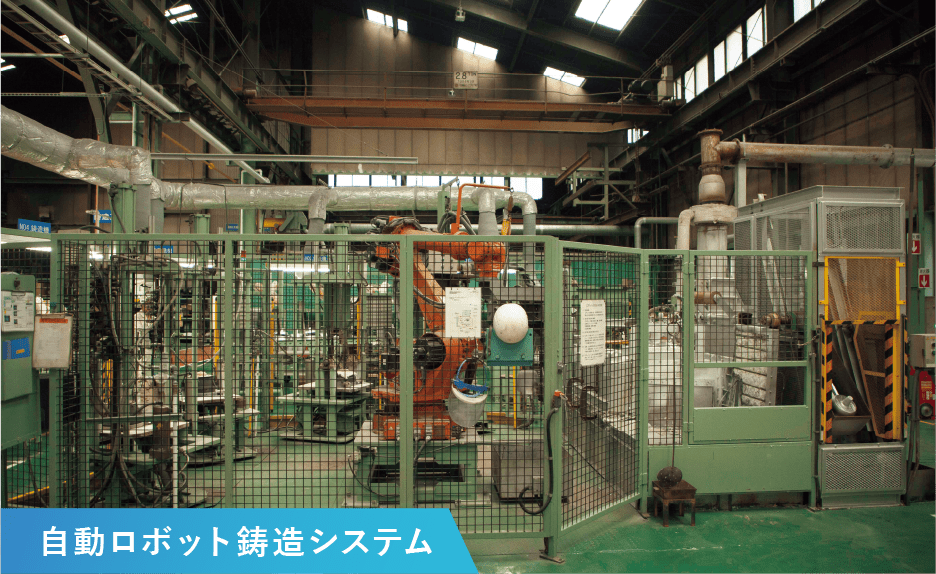

Plastic Molding
Equipped with molding and assembly processes centering on plastic injection molding machines and vibration welding machines, we mold and process a variety of reinforced engineering plastics. Since the early days of developing these products, we have worked to create lighter and less expensive automotive parts for intake manifolds and head covers in order to contribute to automotive performance. Our plastic molding technology, which makes full use of various joining technologies such as press-fitting and vibration welding, as well as the plastic multi-shell process that requires no machining, has made it possible to reduce weight by thin-wall molding. We continue to evolve in our quest to provide better products by taking on the challenge of new methods.
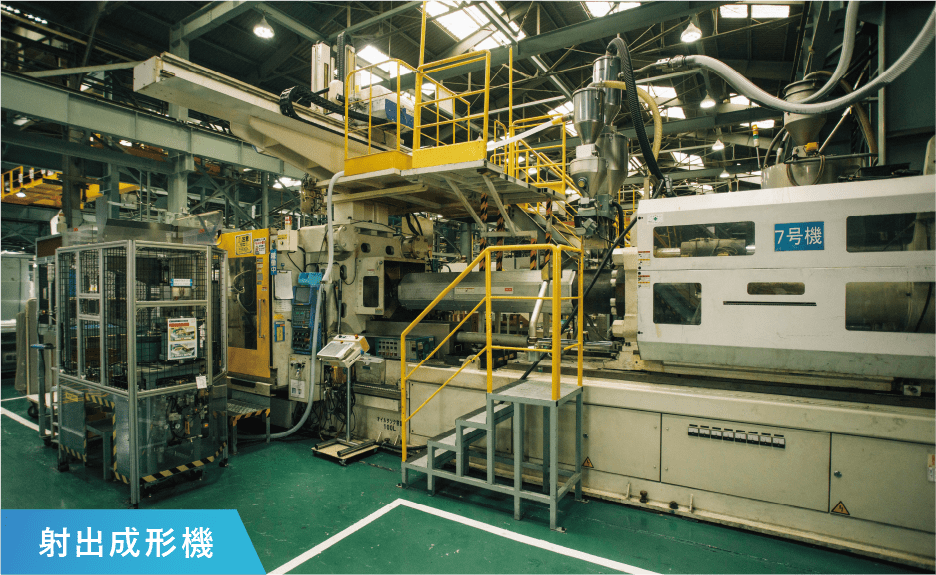
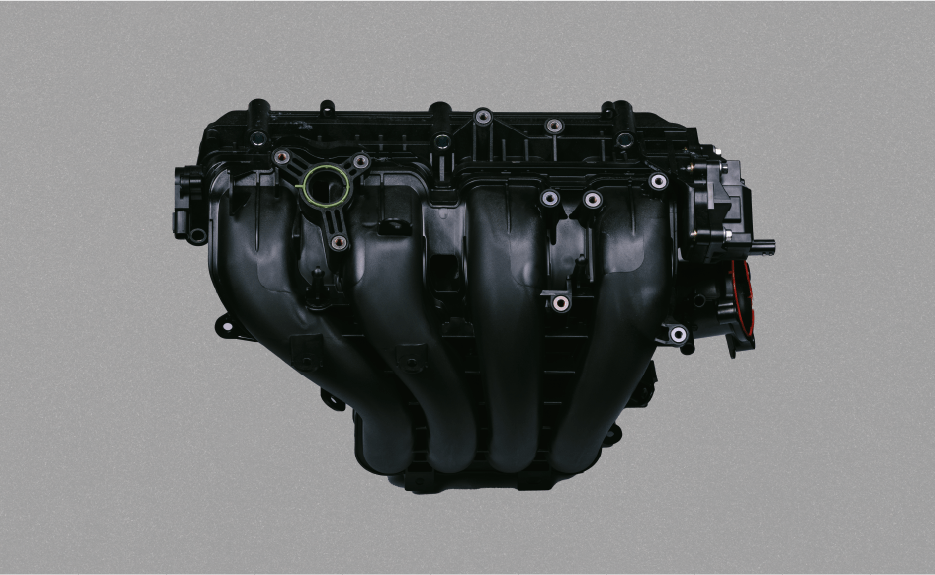
Machining
In addition to various types of foundries, our highly skilled engineers, who are well-versed in a variety of advanced processing skills, perform everything from setting up new processes and modifying existing processes to installing machining equipment and verifying start-up in-house in a short timeframe. As such, we aim for better manufacturing by making full use of IoT and AI to build rational and stable production lines for producing high-quality products, and by striving for innovation and improvement.
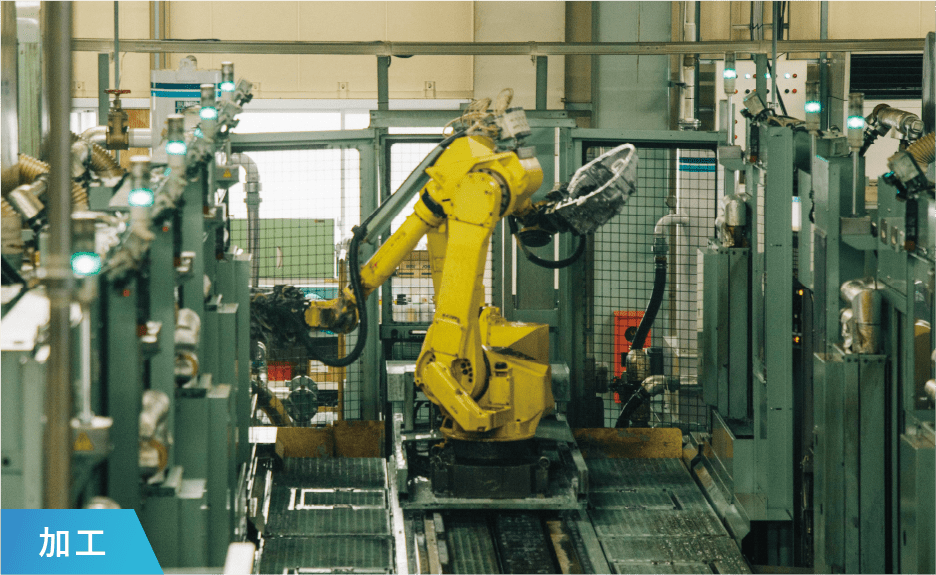
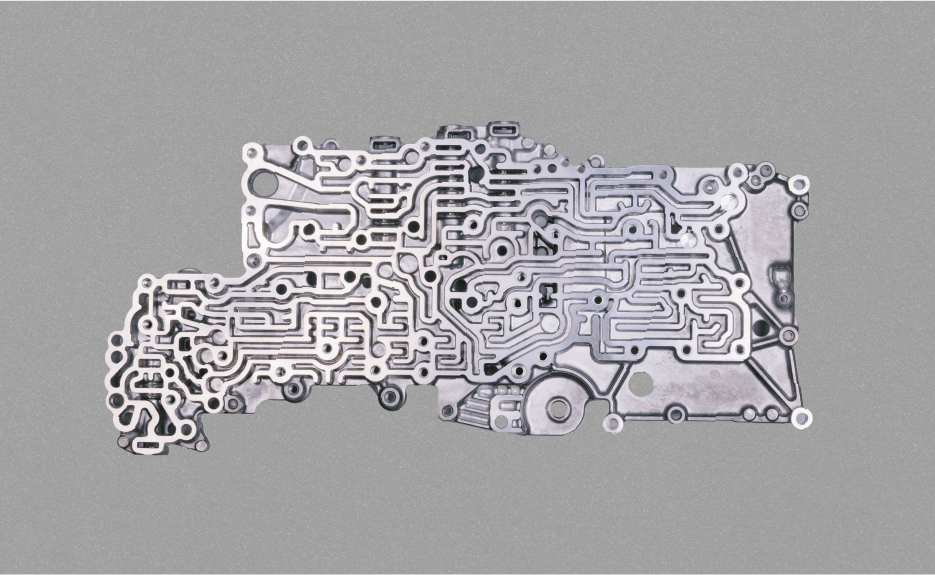
Die Production
Dies are the most critical part of the casting process. Dies are required to maintain uniform product precision, high productivity, and mass production. In order to meet these requirements, we are equipped with a full range of die processing machines, and our highly skilled employees are committed to manufacturing that meets the high expectations of our customers. Our strength lies in our ability to manufacture dies in-house, which enables manufacturing to flow from upstream to downstream without stagnation. This internal environment allows us to respond to any feedback and make prompt adjustments to offer even better products.
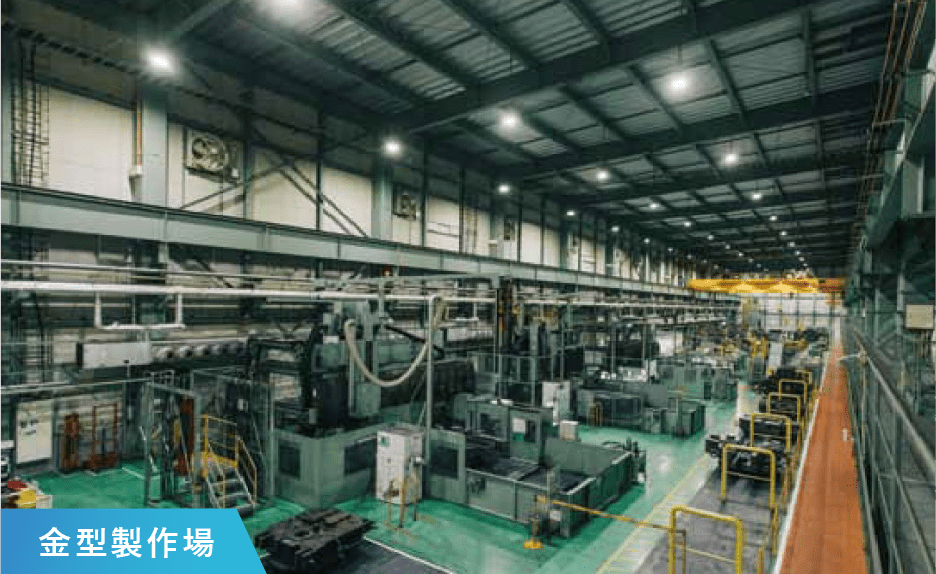
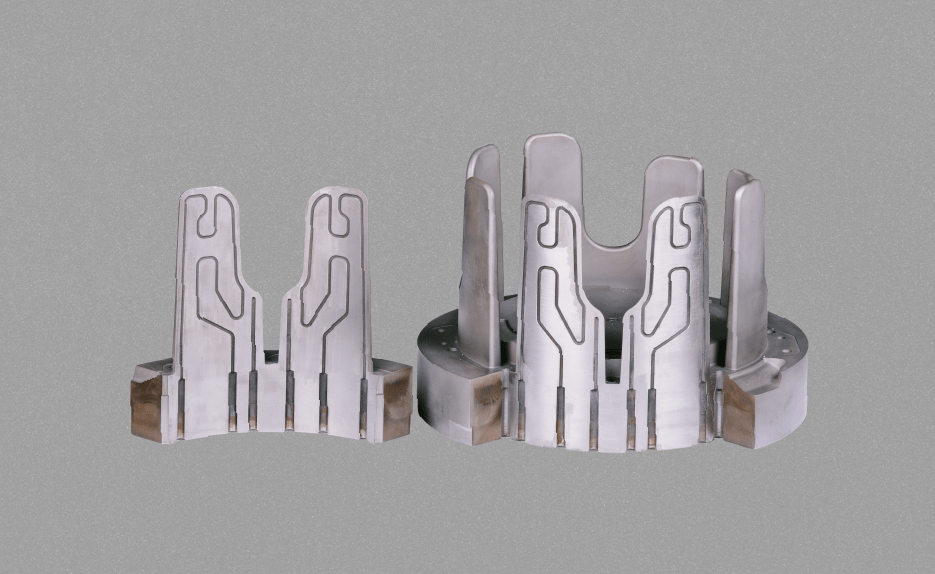